Knife tower CNC vertical lathe
Release time:
2025-04-28
By configuring power cutting tools (such as milling spindles) through the turret, turning milling composite machining can be achieved. For example, when machining aircraft engine blades, mortise and tenon milling can be directly performed after turning the contour to reduce secondary clamping errors.
The turret CNC vertical lathe (referred to as turret vertical lathe) is a high-end equipment in the field of modern mechanical processing. It integrates CNC technology, vertical structure, and turret tool changing system, and is suitable for high-precision and high-efficiency processing of complex parts. The following analysis is conducted from four dimensions: core structure, technological advantages, application scenarios, and selection suggestions:
1、 Core structure analysis
Vertical spindle layout
The spindle is perpendicular to the ground, and the workpiece is directly installed on the worktable to avoid fixture deformation caused by gravity in horizontal lathes, especially suitable for processing large disk and sleeve parts (such as wind turbine bearings and aircraft engine housings).
The vertical structure is convenient for chip removal, and when combined with a fully enclosed protective cover, it can effectively prevent chips and coolant from splashing, improving the safety of the machining environment.
Design of Knife Tower System
Servo power turret: supports automatic switching of multi station (usually 8-12 positions) cutting tools, and can integrate functions such as milling, drilling, and tapping, achieving "one-time clamping, multi process completion". For example, when processing car wheels, a turning tool, milling cutter, and drill bit can be configured on the same turret to complete the composite processing of the outer circle, end face, and bolt hole.
Tool changing speed: The high-end turret tool changing time can be shortened to less than 0.3 seconds, significantly improving processing efficiency.
Tool compatibility: Supports ISO standard tool holders and adapts to multiple tool types.
Numerical Control System Integration
Adopting high-end CNC systems such as Siemens 840D SL and Fanuc 31i, it supports five axis linkage machining (some models are equipped with C-axis indexing function) and can achieve precision machining of complex surfaces such as turbine blades and mold cavities.
Equipped with intelligent compensation functions such as thermal error compensation and reverse clearance compensation, ensuring stable machining accuracy at IT5-IT6 levels.
2、 Technical advantages
High precision and high rigidity
The vertical structure reduces the influence of gravity on the spindle, combined with high-precision linear guides and ball screws, the positioning accuracy can reach ± 0.005mm, and the repeated positioning accuracy is ± 0.003mm.
The spindle adopts NN cylindrical roller bearings, bidirectional angular contact thrust bearings or high-precision angular contact thrust bearings, which can carry a torque of hundreds of Newton meters and meet the requirements of heavy cutting.
Composite processing capability
By configuring power cutting tools (such as milling spindles) through the turret, turning milling composite machining can be achieved. For example, when machining aircraft engine blades, mortise and tenon milling can be directly performed after turning the contour to reduce secondary clamping errors.
Intelligence and automation
Integrated online measurement systems (such as Renishaw probes) can automatically detect workpiece dimensions and compensate for machining parameters.
Support Industrial Internet of Things (IIoT) protocol to achieve device status monitoring, remote diagnosis, and predictive maintenance.
3、 Typical application scenarios
aerospace field
Processing aviation engine disk components (such as high-pressure compressor disks), which are mostly made of high-temperature alloys, requires high rigidity spindles and efficient cooling systems to deal with difficult to machine materials.
Energy equipment manufacturing
Large and complex components such as wind turbine gearbox housings and nuclear power pump bodies require machine tools to have large stroke and high torque output.
Automotive parts processing
New energy vehicle motor housings, gearbox housings, etc. require high-precision multi process integrated processing. The turret lathe can replace traditional combination machine tools, reducing footprint and labor costs.
4、 Selection suggestions
Select based on the size and weight of the workpiece
Large workpieces (diameter>1000mm) require a heavy-duty bed and a high torque spindle; Precision small parts (such as mold inserts) can be prioritized for high-precision wire rail models.
Pay attention to the configuration of the turret
The power turret needs to be matched with the spindle power and speed; Hydraulic turret is suitable for heavy cutting, while servo turret is suitable for high-speed tool changing scenarios.
Evaluate the functionality of the CNC system
Complex surface machining requires support for RTCP (Rotating Tool Center Point) function; Multi variety and small batch production require enhanced programming flexibility (such as support for macro programs and graphical programming).
Consider automation scalability
Reserve robot interfaces, automatic loading and unloading systems (such as truss manipulators), and pallet warehouse interfaces for future upgrades to flexible manufacturing units (FMC).
More information
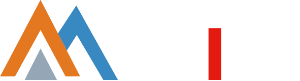
E-mail:meishenmeike@163.com
Zip Code: 215300
Add: No.18,Huangziliang Rd,Qutang Town, Hai'an City,Jiangsu
MEICO
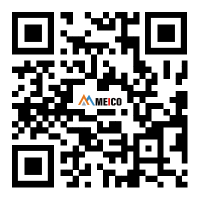
Follow us