One vertical car=3 traditional devices? How does the "space folding technique" of MEICO vertical lathe rewrite the workshop layout?
Release time:
2025-04-29
Performance of the turret: Equipped with a 250Nm high torque hydraulic turret, it supports 12 station power cutting tools and milling functions, achieving combined machining of turning and milling. A single device replaces the traditional combination of lathe and milling machine, saving equipment investment and land area by 30%.
In today's world where the machining error of aerospace components needs to be controlled within ± 0.005mm and the yield rate of new energy vehicle battery shells needs to reach 99.5% or more, traditional machine tools are no longer able to meet the stringent requirements of precision manufacturing. Vertical lathes, with their high rigidity structure, multi axis linkage capability, and intelligent integration, are becoming the core equipment in the high-end manufacturing field.
The Meishen Meike CNC vertical lathe turret machine series, with its three core advantages of high speed, high precision, and high rigidity, provides breakthrough solutions for industries such as military, automotive, and mold manufacturing Solution.
Technological Breakthrough: Precision Manufacturing System from Core Components to System Integration
1. Spindle system: NN series bearings+original imported components, building a high rigidity machining foundation stone
Spindle design: Adopting an enlarged spindle housing and original imported NN series bearings, the axial and radial load bearing capacity is increased by 20%, which can stably support heavy cutting and long-term continuous processing of difficult to machine materials such as titanium alloys and high-temperature alloys.
Accuracy guarantee: Radial runout and axial displacement of the spindle, combined with closed-loop control of the grating ruler, achieve nanometer level positioning accuracy, and meet the high-precision machining needs of aircraft engine blades, hydraulic valve bodies, and other parts.
Efficiency improvement: The maximum spindle speed is reached, and the high-precision servo drive system reduces tool changing time, resulting in a 35% increase in overall machining efficiency.
2. Knife tower system: 250 strong knife tower+modular fixture, reshaping flexible production capacity
Performance of the turret: Equipped with a 250Nm high torque hydraulic turret, it supports 12 station power cutting tools and milling functions, achieving combined machining of turning and milling. A single device replaces the traditional combination of lathe and milling machine, saving equipment investment and land area by 30%.
Fixture Innovation: Optional zero point positioning system and dedicated hydraulic fixtures can be used, reducing the workpiece clamping time from 15 minutes to 3 minutes, with a repeat positioning accuracy of ≤ 0.003mm, suitable for multiple varieties and small batch production scenarios such as new energy vehicle motor housings and hydraulic valve blocks.
3. Bed structure: box shaped inclined body+roller track, overcoming the problems of heavy cutting and chip removal
Rigid reinforcement: The bed body adopts a box shaped structure and Hanna cast iron, with an overall rigidity increase of 50%. Combined with overloaded roller tracks, it can maintain machining stability even under cutting forces of up to 1500kgf.
Chip removal optimization: The combination of inclined bed design and high flow spiral chip discharger achieves an automatic iron chip removal rate of 98%, avoiding precision degradation caused by chip accumulation. It is suitable for processing materials such as cast iron and stainless steel that are prone to producing long chips.
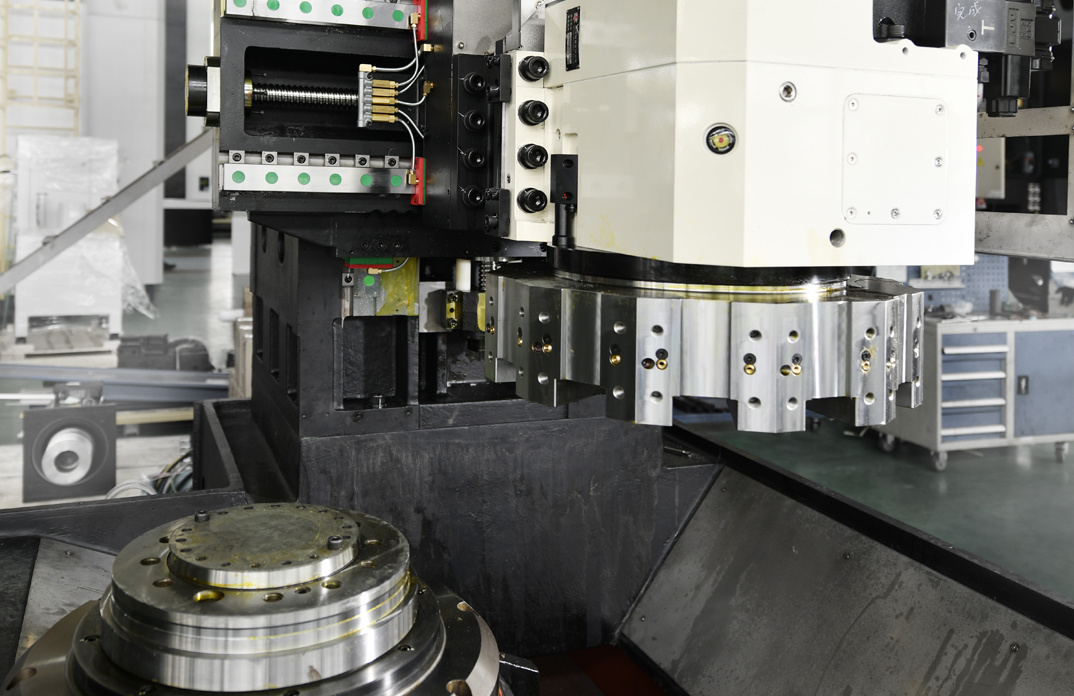
More information
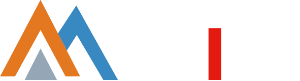
E-mail:meishenmeike@163.com
Zip Code: 215300
Add: No.18,Huangziliang Rd,Qutang Town, Hai'an City,Jiangsu
MEICO
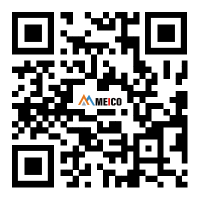
Follow us